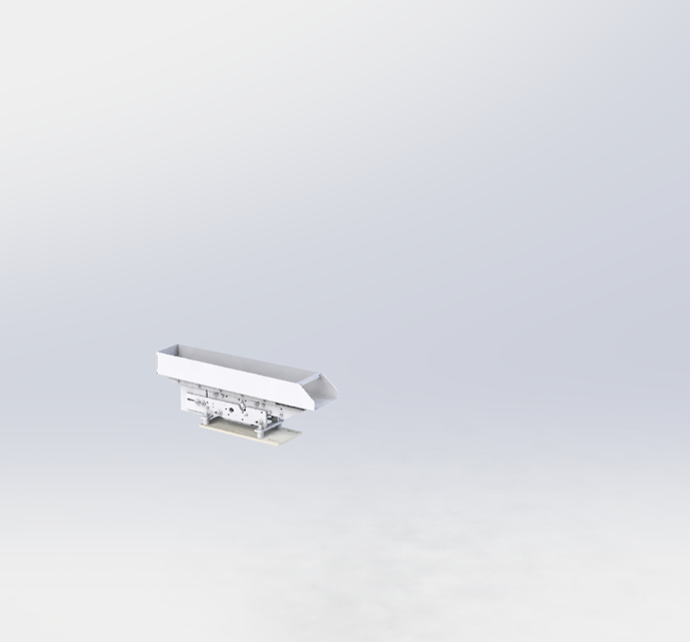
RNA’s VariCube R™ presents a flexible assembly solution that utilises intelligent vibration platforms, coupled with industrial machine vision recognition and a 6-axis robot to feed and assemble component parts of various shapes and sizes.
STEP 2: The FlexCube complete pre-programmed vibratory cycles to orientate and separate component parts, presenting them to an integrated EYE+ vision system for robot pick.
STEP 3: The EYE+ vision system inspects the component parts on the FlexCube platforms and identifies which are laying in a position suitable for being picked. The coordinates are sent to the robot.
STEP 4: A 6-Axis Robot, with suitable end of arm tolling picks all identified component parts and places them in the proper orientation into the assembly nest.
STEP 5: The customisable nest is located by dowels for interchangeability and incorporate part present sensing. An overhead mounted vision system confirms positioning of the component parts before final assembly.
STEP 6: The robot unloads assembled component parts to a storage box via an unload chute.
RNA FlexCube™ flexible vibration feeders offer high performance part feeding, pre-orientation and optimal surface distribution of bulk parts and components.
RNA’s FlexCube™ 3-axis vibration technology allows moving parts freely on a platform in different directions. Systematic part orientation can be achieved with intelligently structured platforms. Using RNA’s intuitive HMI interface, the platform vibration parameters can be tuned specifically for an optimal part distribution and fastest resulting cycle time. A functioning part feeding recipe is typically created in less than 5 minutes.
FlexCube 50 | FlexCube 80 | FlexCube 240 | FlexCube 380 | FlexCube 530 | |
Typical part dimensions | <0.1 - 5 mm | 3 - 15 mm | 5 - 40 mm | 15 - 60 mm | 30 - 150 mm |
A | 14 | 15 | 39 | 252.8 ± 0.5 mm | 369.8 ± 0.5 mm |
B | 60 | 82 | 219.5 | 323.8 ± 0.5 mm | 426.8 ± 0.5 mm |
C | 8 | 9 | 26 | 10 mm | 10 mm |
D | 34 | 52 | 150 | 1.5x45° (4x) | 1.5x45° (4x) |
E | 45 | 65 | 195 | ||
F | 8 | 9 | 14.5 | ||
G | 46 | 65 | 171 | ||
Power supply | 24V / 4A | 24V / 6A | 24V / 8A | 24V / 20A | 24V / 20A |
Platform | precision-manufactured platforms adapted to the parts geometry of parts and the task on hand | |
FlexCube | available with and without backlighting available backlighting: Red / white / green / blue / infrared | |
Communication | Ethernet (TCP/IP), Modbus TCP, EtherNet/IP, EtherCAT, PROFIBUS, SERCOS | |
Software | easy configuration and integration via enclosed operating software | |
Miscellaneous | - input for backlighting for synchronisation with vision system | |
- 2 digital inputs/outputs, e.g. for synchronisation of 2 hoppers | ||
- easy installation on machine table | ||
Options | - Platforms with part-specific surfaces | |
- Calibration plates for robot / vision system | ||
- Quick emptying devices | ||
- Ejection system for quick emptying |
Compatible with all parts geometries: 99% of all parts can be separated by this feeding system, including parts featuring complex outer geometries, and highly fragile parts.
Minimum change-over times: easy exchange of part-specific vibratory plates provides for flexible and future-proof production systems.
Extremely gentle part handling with patented 3-axis vibratory system: Parts can be moved in all directions and flipping parameters can be stored for each specific part.
Free movement of parts in all directions thanks to the use of magnetic coil actuators, for optimal acquisition by camera system with the objective of presenting the parts in the shortest possible time.
No transmission of vibrations to the rest of the line thanks to decoupling of vibratory platform from the casing.
Systematic part orientation using intelligent vibration cycles.
Easy configuration with the feeding software.
Send your message to a member of our team
Read our Privacy Policy to learn how we manage and protect your submitted information.